The potential of mechanical failures leading to catastrophic accidents underscores the critical importance of preventive measures in industries reliant on machinery. Regular maintenance, thorough inspections, predictive strategies, and operator training form the backbone of these measures. However, the real challenge lies in the successful implementation and consistent execution of these preventive strategies. As we initiate this exploration, we will uncover the intricacies of mechanical failures and their prevention, offering insights that could hold the key to transforming your organization’s safety culture and operational efficiency.
Understanding Mechanical Failures
The engineer’s comprehension of mechanical failures serves as the first line of defense in prevention efforts. Understanding the root cause of a failure through a meticulous failure analysis allows for the development of prevention strategies that increase equipment longevity. This analytical process involves examining the equipment’s operational data, maintenance history, and physical condition to discern patterns that may indicate potential failure points.
Subsequently, the information obtained from the failure analysis is utilized to develop a predictive maintenance strategy. This strategy aims to anticipate and address failures before they escalate, thereby enhancing equipment longevity and minimizing downtime. It’s a detail-oriented approach that requires a deep understanding of the equipment’s design and function.
This technical perspective is essential in the decision-making process for determining the appropriate corrective action. It could range from minor adjustments in operation to a complete overhaul of the system. Ultimately, an engineer’s ability to accurately analyze and understand mechanical failures underpins the success of any preventive maintenance program. It’s a strategic approach that generates considerable cost savings over time, reduces the risk of catastrophic failure, and guarantees the consistent operation of critical machinery.
Common Causes of Machine Breakdowns
Machine breakdowns, a dreaded eventuality in any industrial setting, often have several common culprits. Understanding these causes can greatly offset the frequency of such occurrences, and can facilitate more efficient troubleshooting when breakdowns inevitably occur.
One of the most prevalent causes of machinery failure is excessive vibration. Over time, this can lead to wear and tear on machine components, causing them to fail. Vibration analysis is an essential tool in identifying and mitigating this issue. This technique uses sensors to monitor equipment vibrations, isolating any abnormalities that could indicate impending failure. Regular vibration analysis can detect issues before they escalate, allowing for timely maintenance and preventing costly breakdowns.
Operator error also contributes considerably to machinery failure. This can stem from a lack of proper operator training, ill-informed decisions, or simple mistakes. Thorough operator training is, consequently, instrumental in preventing machine breakdowns. Trained operators are more capable of identifying potential issues and taking appropriate preventative measures. They can also operate the machinery more efficiently, reducing unnecessary strain on the equipment.
Risks Associated With Mechanical Failures
While mechanical failures are often viewed as inconvenient disruptions to operational continuity, their implications extend far beyond mere interruptions. The associated risks can be categorized into direct and indirect failure consequences. Direct consequences typically include immediate operational halt, which could lead to significant production losses, ultimately impacting the bottom line. The costs associated with repairs, replacements, and downtime are also direct consequences that can strain an organization’s financial resources.
Indirect failure consequences, however, can be more severe and far-reaching. These can include, for instance, reputational damage when the failure leads to incidents compromising consumer safety. In some cases, mechanical failures can also result in environmental hazards, triggering legal implications and fines.
Risk assessment is an indispensable tool to understand and mitigate these risks. It helps identify potential failure points and their potential impacts, which in turn aids in formulating strategies to prevent such failures. The scope of risk assessment should ideally encompass both the immediate operational aspects and the broader organizational and environmental impact. Through careful risk assessment, businesses can proactively address the risks associated with mechanical failures, enhancing safety, reliability, and profitability.
Importance of Regular Machine Maintenance
The concept of regular machine maintenance is essential in preventing mechanical failures, primarily through early identification and rectification of potential issues. By conducting systematic inspections and timely repairs, organizations can greatly reduce associated costs, enhance the longevity of equipment, and maintain ideal operational efficiency. Additionally, the direct correlation between regular maintenance and the safety of equipment operators emphasizes the integral role preventive measures play in mitigating risks.
Understanding Preventive Maintenance
In order to safeguard the longevity and efficiency of machinery, understanding preventive maintenance proves crucial. This systematic approach incorporates various preventive strategies aimed at mitigating potential mechanical failures. The core of preventive maintenance lies in its anticipation of possible issues, thereby reducing the likelihood of sudden breakdowns and enhancing the machinery’s lifespan.
Preventive maintenance is a multifaceted approach involving several maintenance techniques. Regular inspections form the cornerstone of this process. By routinely examining machinery, potential issues can be detected early, allowing for timely repairs. Lubrication is another critical technique, reducing friction and preventing wear and tear. Cleaning, too, is essential, eliminating any harmful particles that could interfere with the machinery’s performance.
Moreover, predictive technologies play a significant role in preventive maintenance. These include condition monitoring systems, which collect data on machinery operation, and vibration analysis techniques, which detect abnormalities in machinery vibrations. Such technologies facilitate the detection of potential issues before they escalate into serious failures.
Cost Savings From Maintenance
Undeniably, regular machine maintenance offers substantial cost savings in various ways. It enhances cost efficiency by minimizing the frequency of breakdowns, thereby reducing unexpected expenditure on repairs and replacement parts. This preventative approach allows for better budget allocation, with funds being directed towards maintenance rather than unanticipated machine failure costs.
In-depth analysis reveals that the initial investment in regular maintenance can markedly reduce long-term operational expenses. A well-maintained machine operates at a higher efficiency level, decreasing energy consumption and associated costs. Additionally, regular maintenance extends the lifespan of the machinery, deferring the substantial capital expense of machine replacement.
Moreover, maintenance-induced downtime is both planned and brief, as opposed to the potentially lengthy and disruptive unplanned downtime caused by a machine failure. The consequent improvement in production continuity contributes to overall profitability.
Maintenance and Safety Connection
A substantial number of industrial accidents can be traced back to poorly maintained machinery. These mishaps often result from overlooked wear and tear, substandard components, or inadequate lubrication, all of which are avoidable with regular maintenance.
The connection between maintenance and safety is essential. Maintaining machines not only guarantees their best performance but also safeguards the wellbeing of operators. Properly functioning machinery is less likely to malfunction or break down, reducing the risk of accidents and injuries. As a result, adherence to safety protocols is intertwined with the practice of regular machine maintenance.
The implementation of maintenance training is another key aspect. Training equips staff with the knowledge to inspect, detect, and rectify potential issues before they escalate into serious problems. It also helps them understand the importance of complying with safety regulations and emphasizes the role of maintenance in preventing accidents.
The safety protocols and maintenance training, when combined, create a safer working environment. They enhance the longevity of machinery, improve operational efficiency, and most importantly, minimize the risk of accidents. Consequently, regular machine maintenance is not just a preventive measure but a significant safety strategy within the industrial sector.
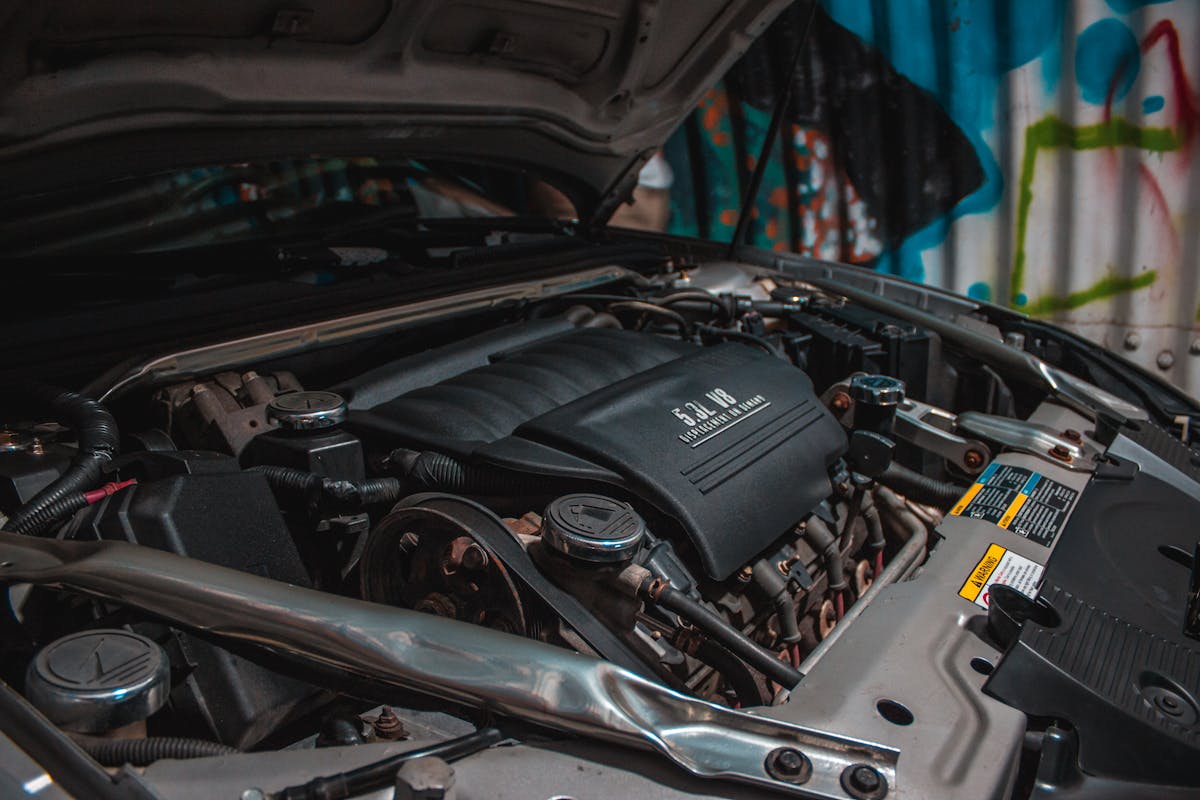
Steps for Effective Mechanical Inspections
Conducting effective mechanical inspections serves as an essential preventive measure against mechanical failures. These inspections, which leverage various inspection techniques and mechanical checklists, help to identify potential problem areas before they escalate into full-blown failures.
The first step in conducting an effective mechanical inspection is to develop a thorough mechanical checklist. This checklist should detail every component that needs to be inspected, including the specific inspection techniques that will be used for each component. This guarantees a systematic and exhaustive approach to the inspection process.
Next, the inspection techniques used should be appropriate for the specific mechanical system being inspected. Techniques can range from visual inspections to more complex methods, such as vibration analysis and thermography. Each technique has its strengths and limitations, and understanding these can help guarantee the effectiveness of the inspection.
Finally, the inspection process should be conducted by trained personnel who understand the intricacies of the mechanical systems they are inspecting. This not only increases the accuracy of the inspection but also enhances safety during the inspection process.
Implementing Preventive Maintenance Programs
As we shift towards the topic of implementing preventive maintenance programs, it is essential to understand the concept and implications of preventive maintenance. The benefits of regular checks and inspections in mitigating mechanical failures cannot be overstated. Furthermore, the optimization of maintenance schedules plays a pivotal role in ensuring the longevity and efficiency of mechanical systems.
Understanding Preventive Maintenance
Nearly all mechanical failures can be mitigated or altogether avoided with the correct implementation of preventive maintenance programs. Understanding these programs is paramount to preventing accidents and ensuring the longevity of mechanical systems.
Preventive maintenance refers to a series of planned, regular, and systematic actions aimed at identifying potential problems and correcting them before they escalate into more serious issues. This concept primarily involves two elements: preventive strategies and maintenance tools.
Preventive strategies are the methods employed to keep machinery in ideal working condition. These strategies typically involve regular inspections, cleaning, lubrication, and adjustments. On the other hand, maintenance tools are the equipment used to carry out preventive maintenance tasks. They range from simple hand tools to sophisticated diagnostic machines.
To better grasp the concept of preventive maintenance, consider the following points:
- Regular inspections help identify potential problems at an early stage.
- Maintenance tools aid in the efficient execution of preventive strategies.
- Scheduled services help prolong the lifespan of machinery.
- Preventive strategies help reduce the likelihood of major breakdowns, thereby minimizing production loss.
Benefits of Regular Checks
Regular maintenance checks serve as the foundation of successful preventive maintenance programs, offering numerous benefits that enhance the performance and durability of mechanical systems. A thorough benefits overview reveals that these checks are vital for detecting early signs of malfunction, guaranteeing the functionality of safety features, and reducing downtime due to unexpected failures.
In the domain of mechanical systems, regular inspections play a significant role. They enable technicians to identify potential problems before they escalate, reducing the risk of catastrophic failures and accidents. This proactive approach not only improves safety but also extends the lifespan of the equipment, leading to significant cost savings over time.
Furthermore, regular checks help maintain peak performance levels. They confirm that each component functions at its best, reducing inefficiencies and energy waste. This results in improved productivity and greater return on investment from the mechanical systems.
Optimizing Maintenance Schedules
The cornerstone of mechanical system longevity lies in the enhancement of maintenance schedules, encapsulated in the implementation of preventative maintenance programs. Such systems aim to prevent mechanical failures that can lead to accidents, consequently ensuring operational efficiency and safety.
To achieve this, businesses must harness the power of advanced maintenance technology and scheduling software. These tools allow companies to streamline their maintenance operations, effectively forecasting potential mechanical issues before they develop into critical failures.
- Maintenance technology aids in the collecting and analyzing of data from various equipment, providing valuable insights on performance, wear and tear, and potential areas for enhancement.
- Scheduling software enables the setting up of regular maintenance activities, ensuring that no task is overlooked and that maintenance work is carried out at ideal intervals.
- Implementing predictive maintenance strategies, informed by real-time data, can help identify potential issues before they escalate, thereby avoiding unnecessary downtime.
- Finally, equipment history tracking can provide valuable insights into the lifecycle of machinery, helping to predict and prevent future failures.
Case Studies in Mechanical Failure Prevention
Several compelling case studies underscore the importance of preventing mechanical failures in various industries. A notable example is the airline industry, where rigorous failure analysis is conducted after every incident, leading to the development of more robust maintenance protocols.
In one case, a detailed failure analysis revealed that routine checks had missed a small crack in a turbine blade. The crack eventually led to catastrophic engine failure mid-flight. This incident prompted a review of inspection procedures, leading to the implementation of more sensitive detection methods. The new processes remarkably reduced similar failures, improving overall aviation safety.
Another example can be found in the automotive industry. A renowned car manufacturer experienced repeated transmission failures in one of its popular models. Failure analysis identified a design flaw in the transmission system, which was not compatible with certain driving conditions. The manufacturer initiated a recall, rectified the flaw, and enhanced its design validation processes.
These case studies highlight that understanding the root cause of mechanical failures is essential for prevention. Investing in sophisticated failure analysis techniques can lead to noteworthy improvements in safety and reliability. Furthermore, these case studies also emphasize that failure prevention is not a one-off task, but a continuous process requiring vigilance and commitment.
Frequently Asked Questions
What Are the Costs Associated With Mechanical Failure Repairs?
The costs associated with mechanical failure repairs involve both direct and indirect expenses. Direct costs include parts and labor, while indirect costs encompass downtime losses. Effective repair strategies and thorough cost analysis can mitigate these expenses.
Can Mechanical Failures Affect the Lifespan of a Machine?
Yes, mechanical failures can greatly impact a machine’s lifespan. Regular machine maintenance and performance optimization are essential in minimizing these failures, therefore enhancing the machine’s longevity, efficiency, and overall operational quality.
How Does Weather Impact Mechanical Failures?
Weather conditions considerably impact mechanical failures as extreme temperatures can affect machinery’s performance. Seasonal maintenance is essential to counteract these effects, ensuring ideal component function and reducing the risk of unexpected breakdowns.
What Role Does Operator Training Play in Preventing Mechanical Failures?
Operator training plays an essential role in mitigating mechanical failures. By enhancing operator proficiency through thorough training programs, operators can identify and address potential issues, thereby reducing the likelihood of equipment failure and subsequent accidents.
Are There Industry-Specific Guidelines for Mechanical Failure Prevention?
Yes, industry-specific guidelines for mechanical failure prevention exist. Industry standards and safety regulations are established to minimize risks, ensuring regular inspections, maintenance, and adherence to operational protocols to prevent mechanical failures.